03 Mar Two-Week Advanced Blacksmithing Class Returns: An Interview with Tal Harris
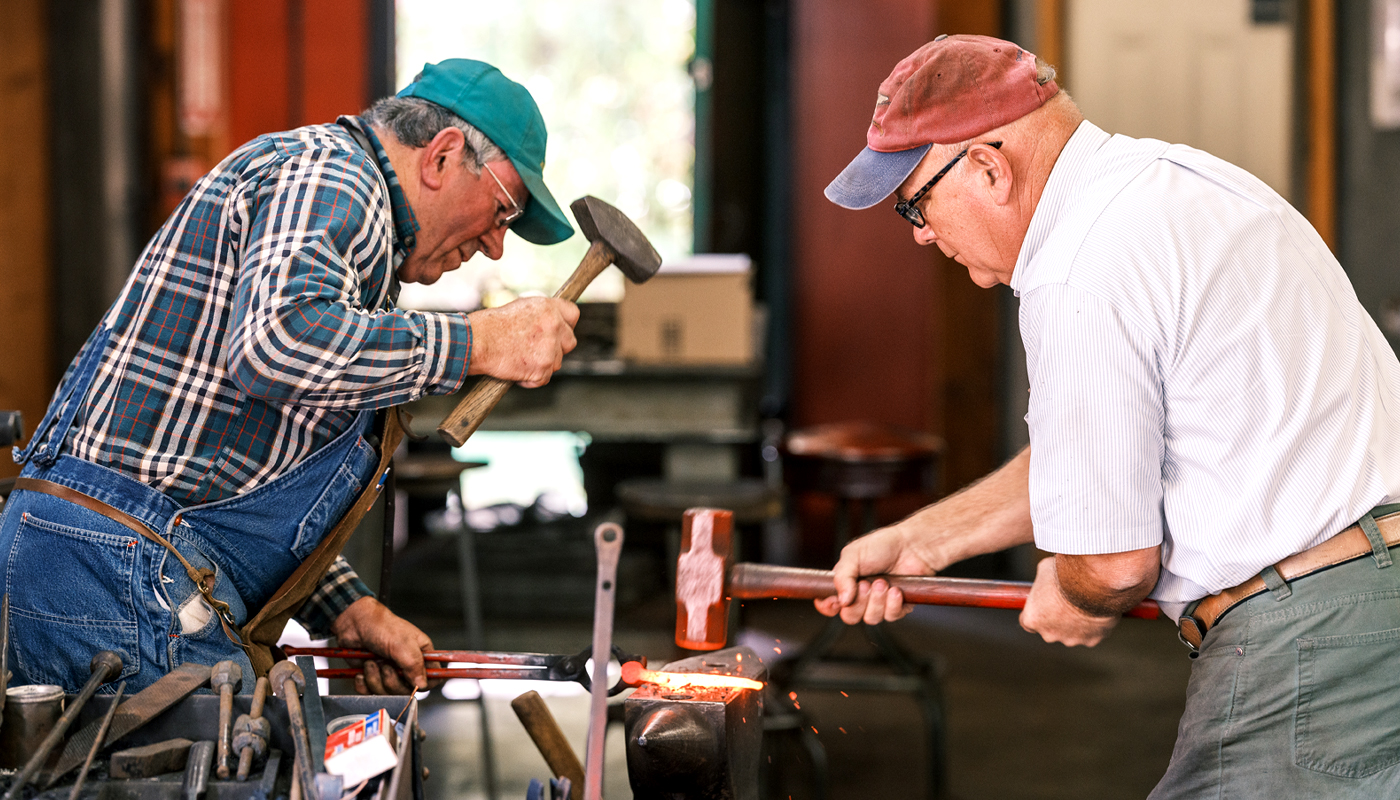
Jimmy Freeze & Tal Harris Forge Welding Class Demonstration
We are so excited that Advanced Blacksmithing, a two-week intensive class for experienced blacksmiths, returns to the Folk School this September 8th through the 21st. Tal Harris and Clay Spencer are teaming up to bring back the legacy of master blacksmith Francis Whitaker, who taught this class format at the Folk School from the 1970s to 1997.
In this unique class, students will have the opportunity to focus on fine ornamental iron work for a personal, predesigned project. In addition to working on individual projects, students will share and learn from the techniques used in their fellow classmate’s work. If you are a seasoned blacksmith, don’t miss this opportunity to immerse yourself in a learning environment surrounded by your peers and led by two master blacksmiths who have been part of the Folk School blacksmithing community for over 3 decades. Register today!
We talked to Tal Harris about Advanced Blacksmithing, the history of blacksmithing at the Folk School, and learned more about his experience. Enjoy our interview!
Notice: This Class Has Passed. Please check out our other Blacksmithing classes.
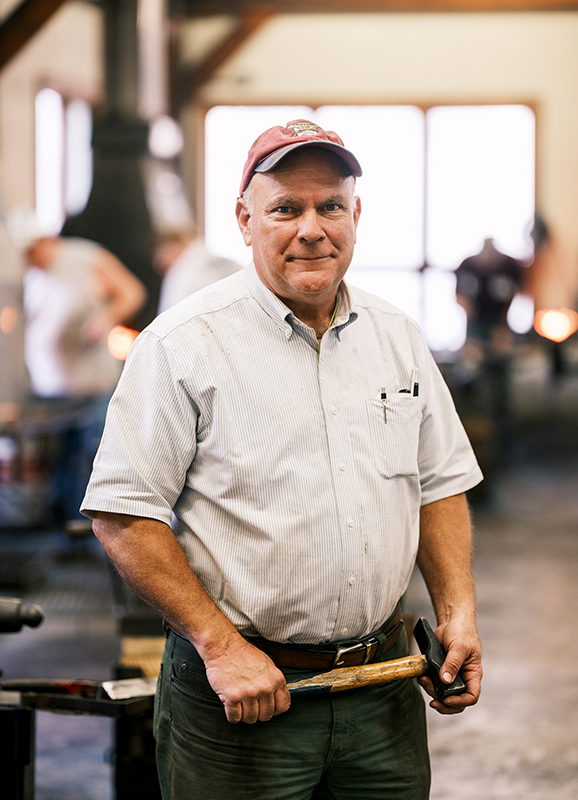
Tal Harris in the Blacksmith Shop
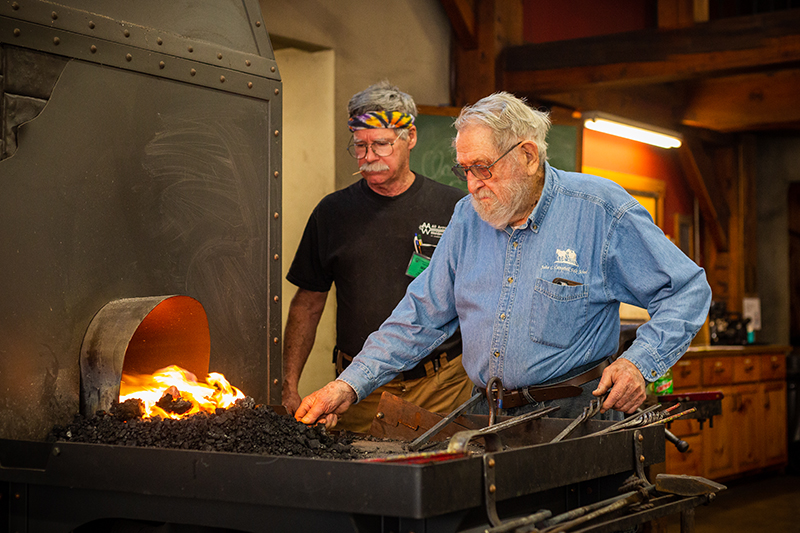
Mike LaMarre & Clay Spencer at the Instructor’s Forge
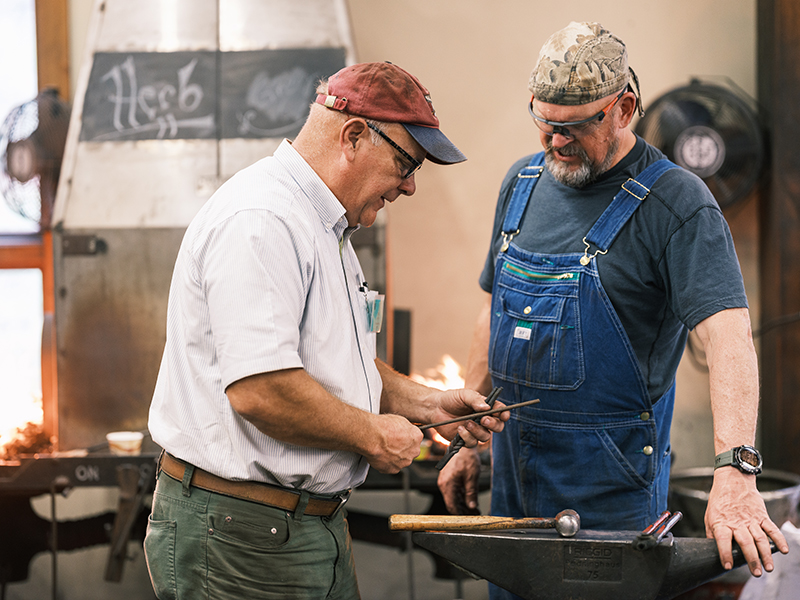
Tal Harris & Greg Collins in Forge Welding Class
CP: Your upcoming class, Advanced Blacksmithing, co-taught with Clay Spencer, is scheduled for September 8-21, 2024. This is a rare two-week format, but this format is not new to the Folk School. Can you talk about the legacy of this class and why you and Clay decided to return it to the curriculum now?
TH: Francis Whitaker started the two-week advanced classes in the late 1970s, eventually teaching two per year. Francis taught his last one in 1997, overlapping with Clay for several years prior. Clay continued teaching the class for several years, and at some point, it was no longer offered.
It has long been a desire of mine to see the class reintroduced. The projects are more involved, lots of problems to work through and everyone learns. This one will be special as Clay and I were both students of Francis and will be passing on his techniques, and his high standards for precision architectural ironwork.
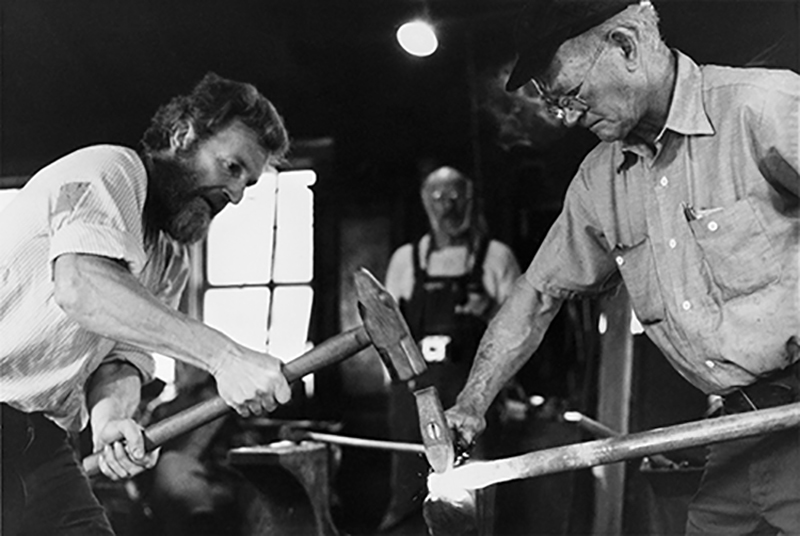
Jim Kroeplin & Francis Whitaker (1978)
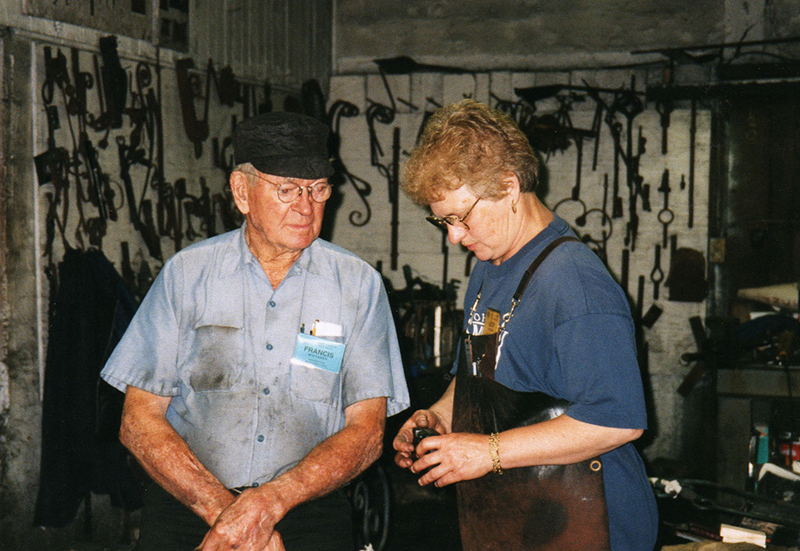
Francis Whitaker & Judy Berger (1997)
CP: Who is the ideal student for Advanced Blacksmithing?
TH: Francis’s basic expectations were students be able to make a free-hand scroll, a drop-the-tongs forge weld, and make an upset square corner in square stock. Those skills, plus a sincere desire to forge decorative items using traditional techniques are what we are looking for in a potential student.
CP: Besides the time-length, will other Francis Whitaker traditions be emphasized? Will this class also focus on his ethos and style?
Yes, both Clay and I learned from Francis, and many techniques will be shared during the class.
Precise layouts to a scribed line, making test pieces to determine material movement, and accurate execution will all be key aspects of the class. Full-scale detailed drawings are required, showing every rivet, collar, etc. This allows most problems to be solved on paper, which is easier than in iron.
CP: Why is two weeks an ideal format?
TH: In keeping with past Advanced Blacksmithing classes, projects tend to be more involved. Fire screens, baker’s racks, gates, furniture, and other more involved items have been accomplished during the class. The classes are exciting. The momentum, creativity, and sharing of information is amazing. Everyone learns. Clay and I will learn.
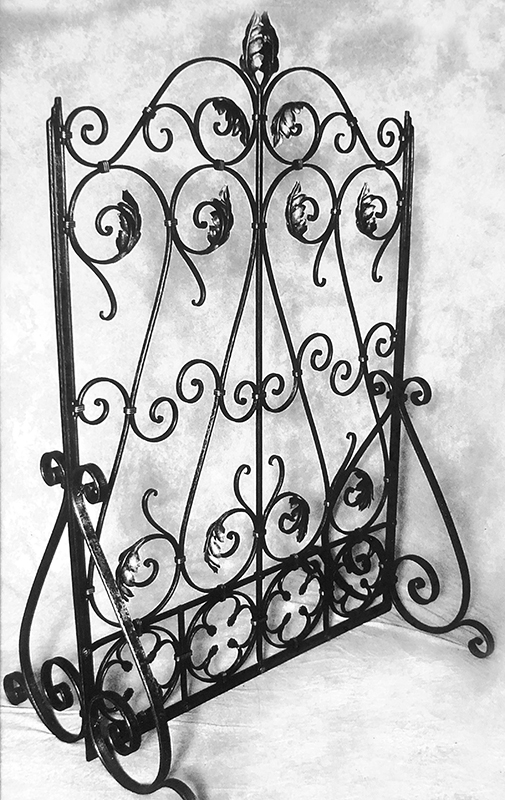
Ironwork by Tal Harris
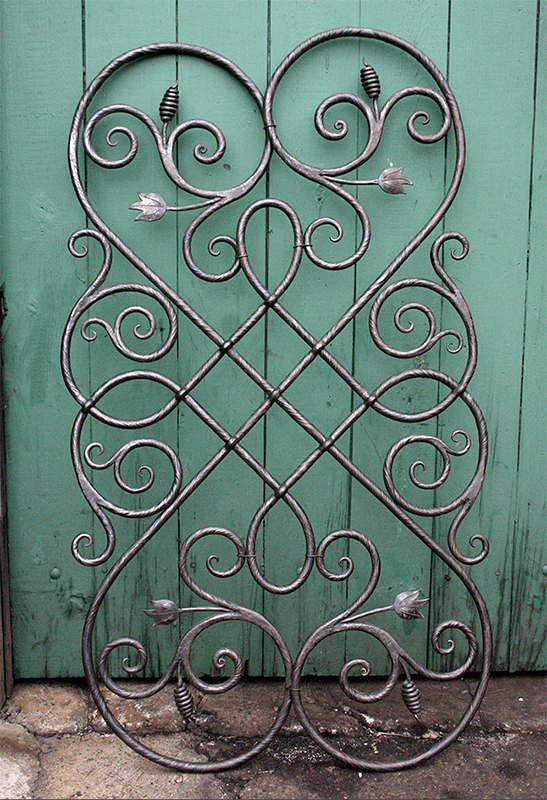
Ironwork by Tal Harris
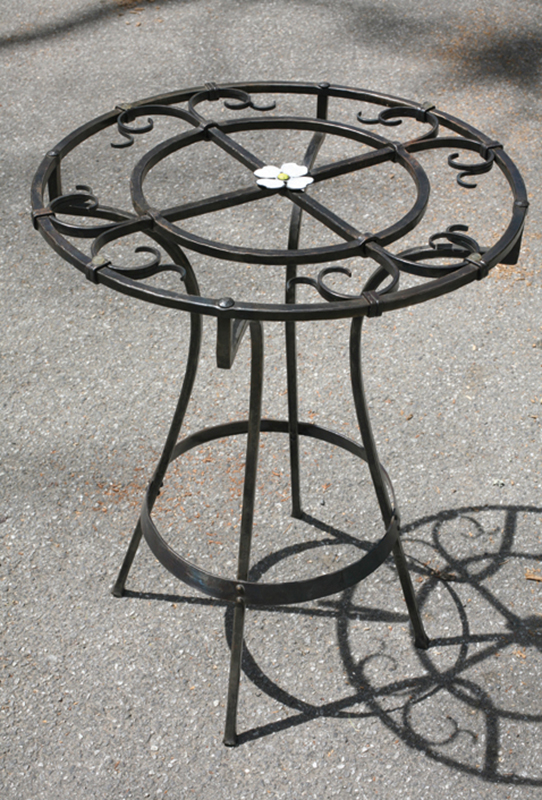
Table by Clay Spencer
CP: According to your class descriptions, students must arrive with a pre-designed and pre-submitted project. What should students consider when planning a project?
TH: The main constraint on the projects is time. An elaborate lock could easily consume the entire two weeks. A much larger garden gate of a simple design should be easily achievable. As students design projects; materials, tooling to forge joinery and other details, all need to be worked out.
On a personal note, in 1992, when I was enrolled in what was billed as Francis’s last class, I spent many hours making every tool required, using The Blacksmith’s Cookbook as the guide. Had I waited until I arrived at the Folk School to do this, there is no way I would have completed the project.
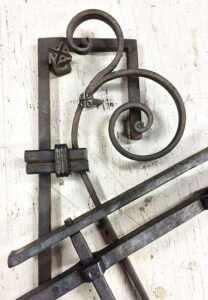
Ironworks Details by Tal Harris
CP: How did you get started in blacksmithing?
TH: While an Industrial Arts student at ASU, Tom Perrin, who was a graduate assistant, brought a coal forge and anvil into the metals shop for a demo for his class. I spent most of my time in the metals shop, so I was able to see Tom’s demo and all the nice ironwork he brought. I immediately knew this was something I really wanted to do.
Tom had been a 1970s student at Turley Forge and encouraged me to take Frank Turley’s 6-week beginner class. My uncle Buster paid the tuition as an ASU graduation present. I received a power hammer from my dad. My future wife Kim and I left for Santa Fe the day after graduation.
While at Frank’s we were encouraged to play hooky and attend a conference for the South West Artist Blacksmith Association (SWABA) at Russ Swider’s shop in Rowe, NM. The demonstrators I remember were Tom Joyce, Alfred Haberman and Francis Whitaker. I briefly met Francis and acquired his demo piece. I kept in touch with Tom Perrin after graduation and he attended an Advanced Blacksmithing class at the Folk School with Francis. He encouraged me to take the Advanced class.
CP: When did you first come to the Folk School?
TH: I first visited the Folk School in the early 80s, attending joint meetings of NC and AAC, demos, and blacksmith auction. Francis would often be a demonstrator and the meeting and auction were on the middle weekend of the two-week class.
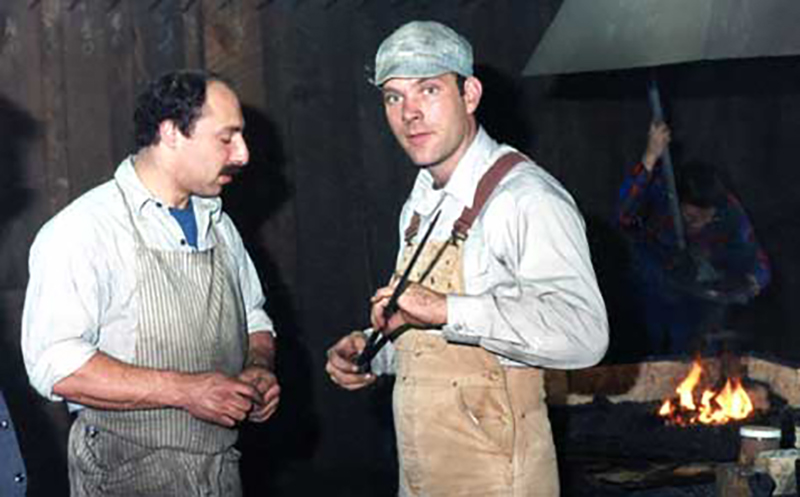
Peter Ross and Tal Harris in the Shop in 1988
CP: Why do you like teaching at the Folk School?
TH: Sharing traditional blacksmithing techniques and processes is important. Every class is a learning experience, for both the students and instructor. I enjoy working through problems with a class. Passing along what others have shared with me, working out solutions to problems, in the environment of the Folk School; it just doesn’t get any better.
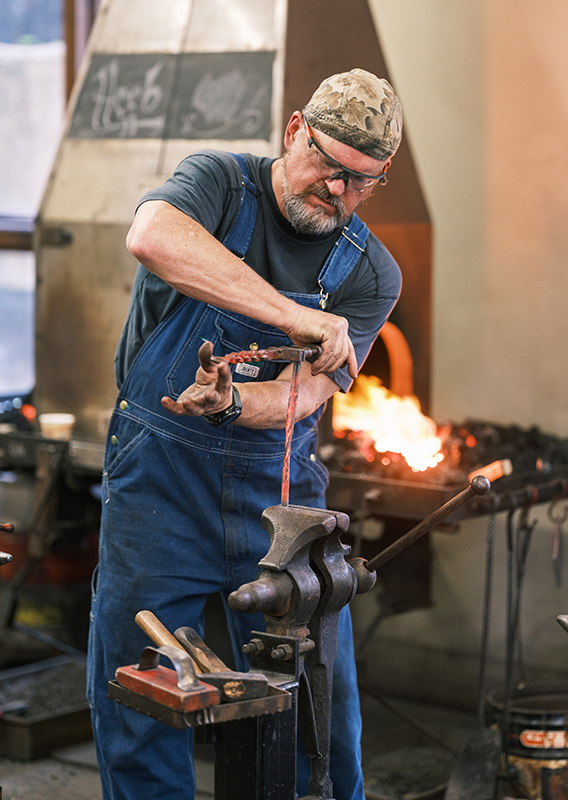
Student Greg Collins in Tal’s Forge Welding Class
CP: The blacksmithing renaissance in the 1970s is a reason that Francis Whitaker shifted focus more to imparting his knowledge on younger generations. Francis has referred to himself as “a link with the past,” dedicating the last 30 years of his life to teaching at places like the Folk School and Colorado Rocky Mountain School. Do you see a similar resurgence of interest in blacksmithing occurring now? Or do you think it has been going strong since the 70s?
TH: There is definitely a resurgence of interest in bladesmithing. I attribute a large part of this to the TV show Forged in Fire, which focuses on blades. Based on ABANA Chapter conferences and ironwork posted on social media I have seen growth in membership and steady and marked advancement in the quality of ironwork over the years.
CP: You have referred to your most common bond with Clay Spencer to be your shared appreciation for Francis Whitaker and the blacksmithing knowledge he so freely offered. Sharing information and passing on traditions seems to be a crucial element to preserving and encouraging the future of blacksmithing. How do you see yourself as a participant in this legacy?
TH: In the 1992 class, my project was a window grille that included many elements of traditional architectural ironwork that I had never done before, all of which were found in Francis’s Blacksmith’s Cookbook.
I had wanted to take Francis’s Advanced Blacksmithing for several years and believed this would be my last chance to do so. Even though we had briefly met in 1982, those two weeks were the first time we actually got to know each other on a personal level.
There were only a handful of students in that class, so all enjoyed a greater percentage of Francis’s time. I spent many hours reading his book, thinking through the project, making the tools he recommended for the various tasks, and preparing as best I could to learn as much as possible. There were questions I had after reading his book multiple times and during the two weeks we were able to discuss each of these, some of which Francis took time to demonstrate, pieces I still have.
The project was successful and the relationship began. Over the next few years, we would share ideas, mostly by mail, as he wasn’t much of a conversationalist on the phone. He would usually bang out a letter on his portable typewriter, make a sketch, and sign it “Francis.” The folder of those letters is about 2 inches thick and something I read through every so often.
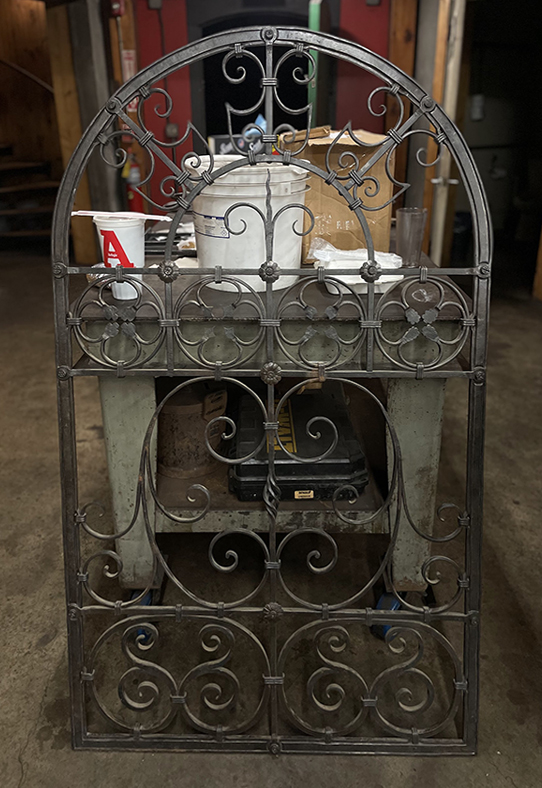
Round-top Window Grill
Tal’s Project Forged in Francis Whitaker’s Advanced Class (1992)
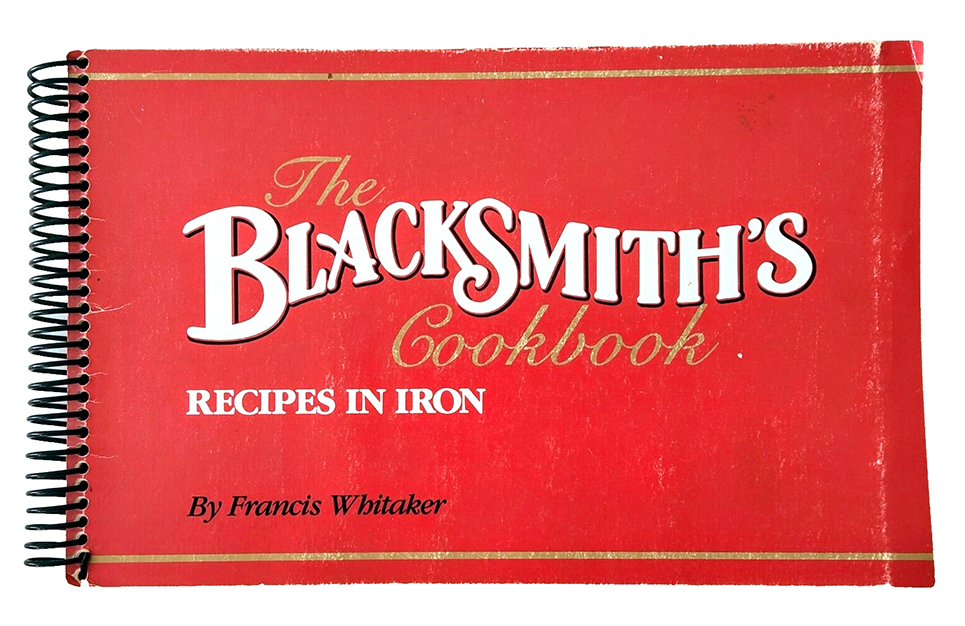
The Blacksmith’s Cookbook by Francis Whitaker
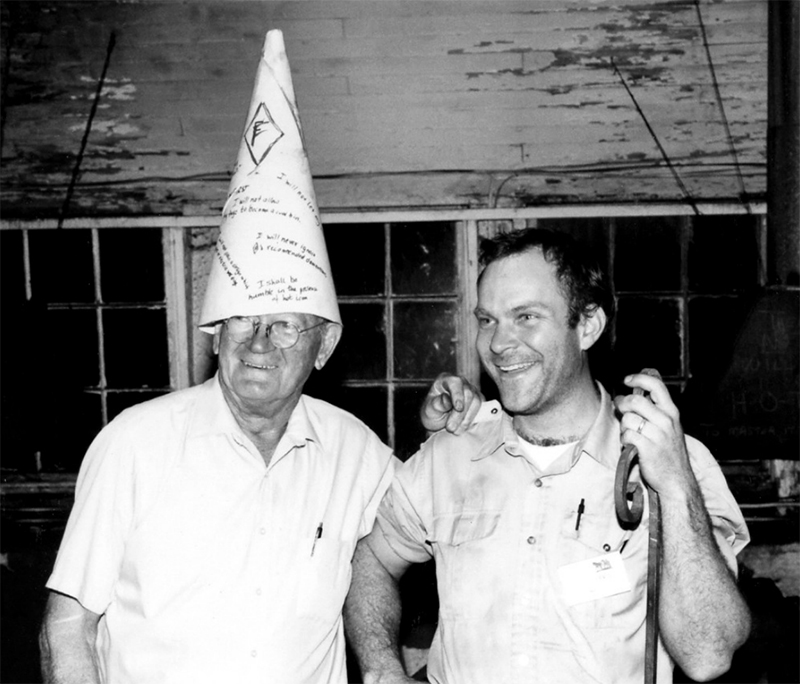
Francis Whitaker & Tal Harris (1992)
After that first two-week class, there were other opportunities to spend time working with Francis. 1994 ABANA Ring Project, 1995 David Berger (Judy Berger’s son) and I spent a week with Francis in Carbondale. Francis’s only request was “bring a project”. In the evenings, I would take time to look through his tool room, every drawer, cubby hole and shelf from top to bottom. There were iron samples hanging all over the shop, some he made and some historical pieces.
In 1996, I again participated in the ABANA Conference project with Francis leading the team. 1997 was the year Francis made a return trip to the Folk School, which was his last two-week Advanced Class. Clay was assisting and there was a full roster of 12. The project chosen for this week was a difficult grille, designed partly as a challenge and learning opportunity but mostly as a tribute to Francis, in a way thanking him for sharing his knowledge.
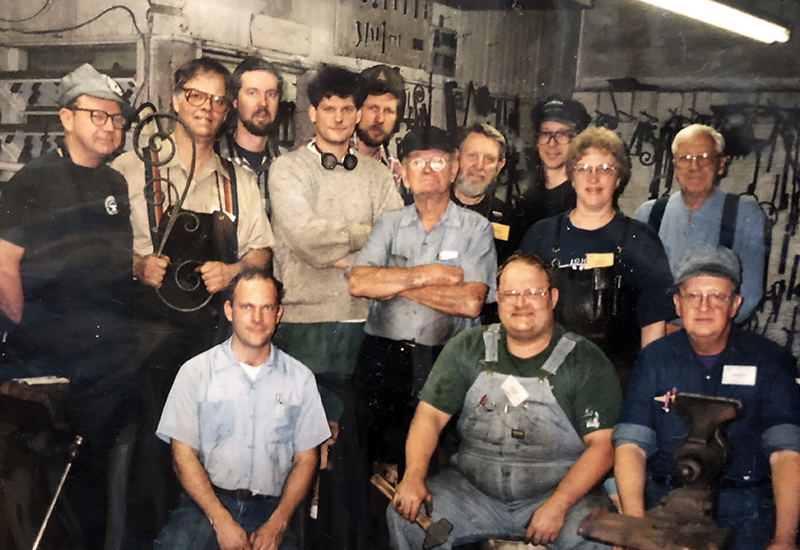
Francis Whitaker’s Last Two-week Advanced Folk School Class in 1997. Can you spot Tal & Clay?
After this last class, Francis was able to attend the 1998 ABANA Conference in Asheville, NC. He attended my demo which was a great treat. At the 1999 Rocky Mountain Smiths conference, I was Francis’s striker at his last demo (and my pants caught fire). He passed away about 2 months later.
Those 7 years I was able to learn from Francis helped prepare me to continue his teachings and participate in that aspect of his legacy. I returned to Carbondale and led the Master Class at RMS in Carbondale. Teaching the things he taught me, in his shop, with his tools and equipment. Doesn’t get better than that.
CP: What do you remember about Francis as a teacher?
TH: He was direct. He expected students to learn his techniques. Taking notes during demos was expected. If you forged something, had trouble, and went to him for advice, the first question was usually “how did you do this?”. If the student sort of followed his demonstration, he would ask “did you write it down?” A “no” might prompt a second demo, or at least clarification of what was missed. Francis had little to no tolerance for those who would not listen, take notes, and follow proven methods. That said, I’ve seen him adapt when he recognized a technique as better than his own.
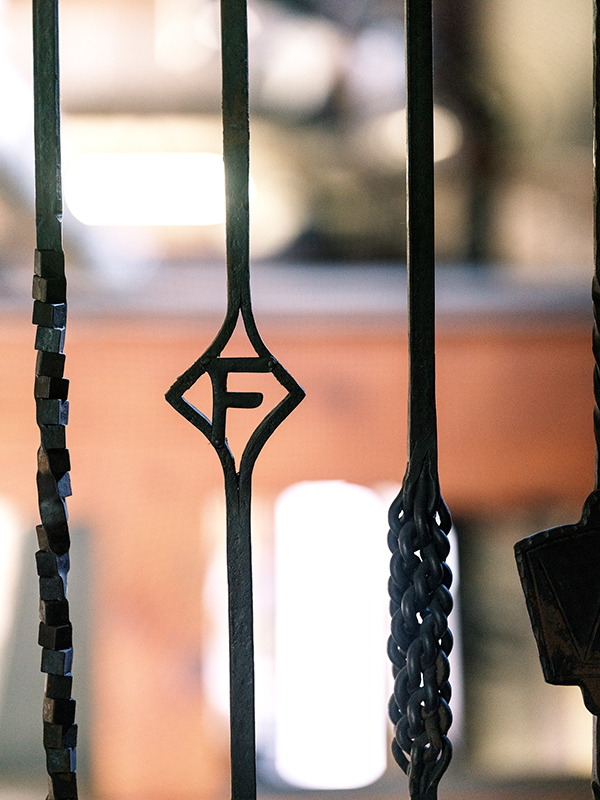
Memorial Picket Created by Tal, Featuring Francis’s Signature “Diamond F.”
CP: Tell me about the memorial picket (with the diamond shape with the F in the center) that you made to honor Francis. Where can folks find this when touring the shop?
TH: The picket has elements taught by Francis. A slit and drifted hole, a twist that he enjoyed demonstrating, contained in the hole which is enclosed by riveted front and back covers are a portion of Francis’s cremains. The picket is located on the landing at the top of the spiral staircase, appropriately overlooking the instructor’s forge.
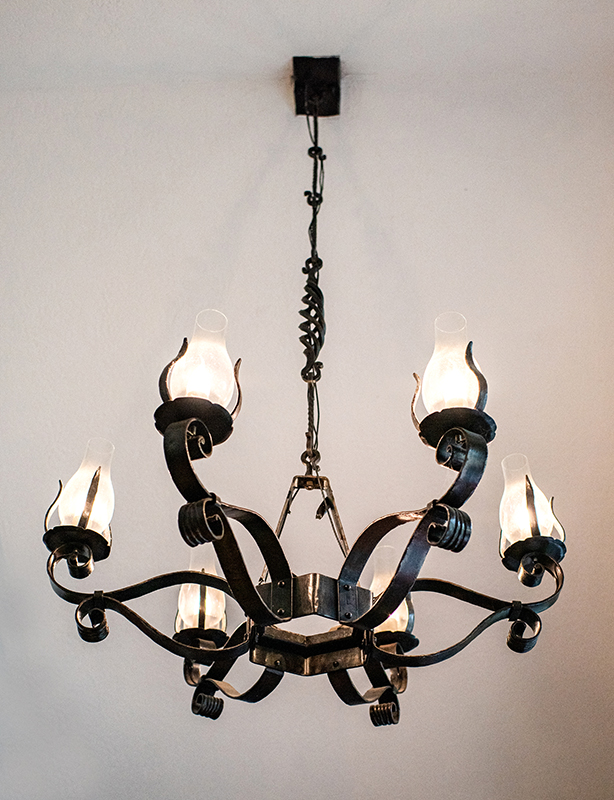
Chandeliers can be found in the Dining Hall and classroom upstairs in the Blacksmith Shop.
CP: Were you and Clay involved in the creation of the Dining Hall chandeliers or the Whitaker shop sign?
TH: Clay was involved in the chandelier project for the Dining Hall. Clay also led the work week to construct the Whitaker shop sign. My wife Kim and I both participated that week. I made the branching scrolls, Kim and Judy Berger made the two cats, which represented Francis and his wife Portia. Besides the Whitaker sign, I contributed to the Red Railing project which was led by Bert Smith.
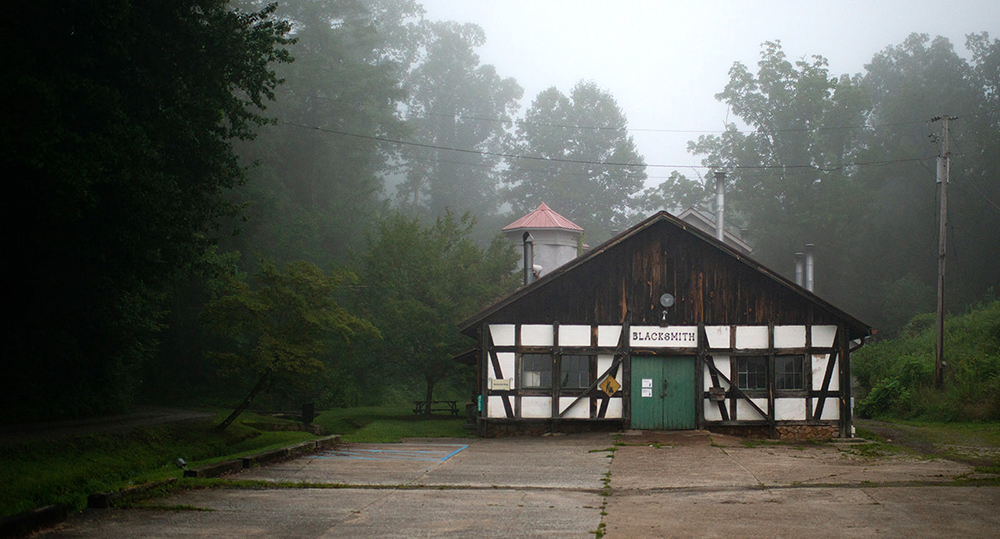
The Francis Whitaker Shop was originally the Folk School Dairy Barn are served as out main shop for many decades. Now the forges are in the new Clay Spencer Blacksmith Shop and the Whitaker Shop is primarily used for welding, finishing, and design space.
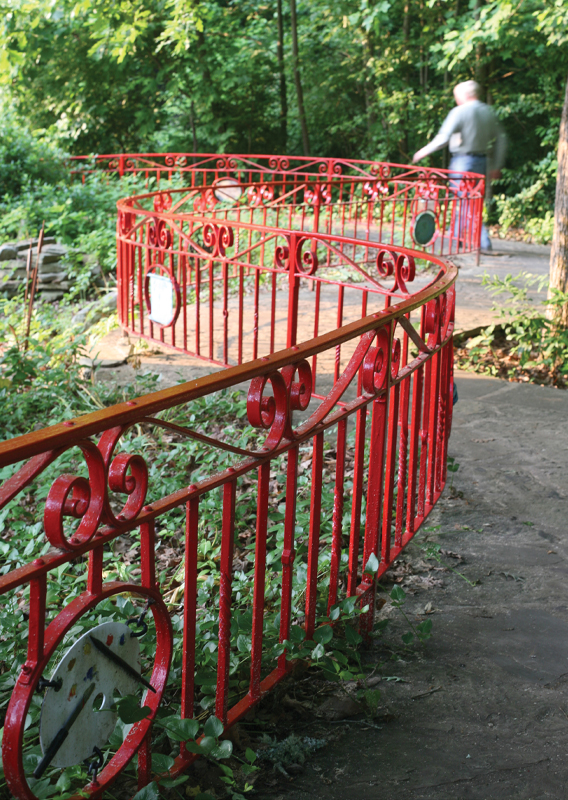
Our Iconic Red Railing by the Dining Hall. Bert Smith led the team to build this during several Blacksmith Work Weeks.
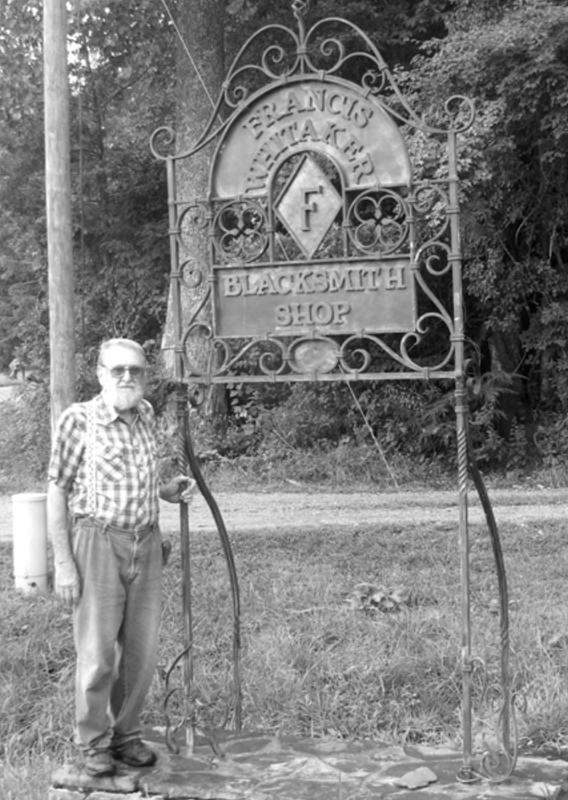
Clay & Whitaker Shop Sign
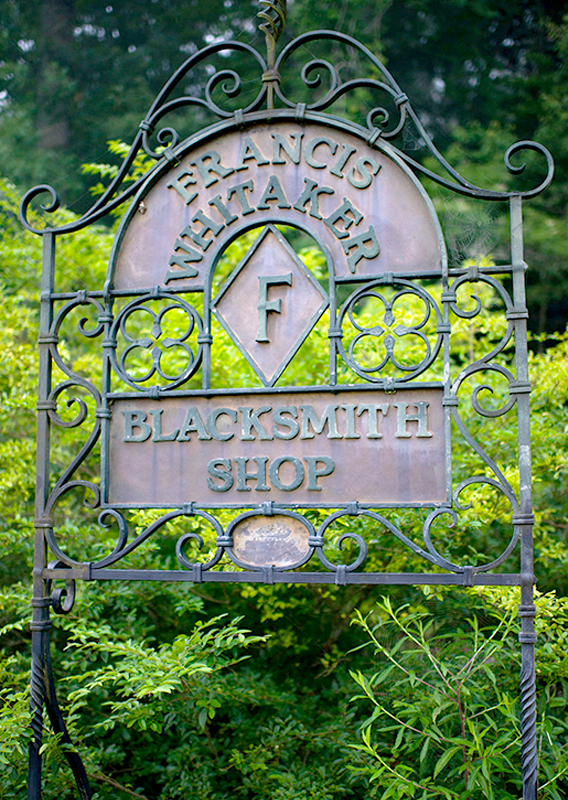
The shop sign was created in 1994 during Blacksmith Work Week.
CP: Both you and Clay worked professionally in the aerospace industries. Coincidence? Or is there a more meaningful connection between aerospace, metal, and blacksmithing? How does one inform the other?
TH: The fact that Clay and I both worked in Aerospace is coincidental. There is a connection between blacksmithing, the metals industry and aerospace. The company where I work melts, forges, rolls and finishes a variety of nickel, iron and titanium-based alloys. I’ve been able to see hot metal almost every day of my 40+ year career.
There are several parts of our forging process that are directly relatable to blacksmithing. The way large diameter material is cut hot is exactly like using a hardie and a hammer, only much larger. Blacksmiths were the original forgers of metals. Modern forge shops shape all manner of metals that have taken man to the moon and exploratory vehicles to other parts of the solar system.
CP: What advice do you have for someone who wants to pursue blacksmithing at a professional level?
TH: Don’t allow the a vocation you enjoy to become a vocation you dread. If traditional architectural ironwork is what gives you joy and personal satisfaction, having to make 1000 J hooks to pay the bills might not be too satisfying.
A person really needs to think realistically long and hard about making this transition. What is my skill level? What are my target markets? Am I equipped to be efficient in supplying those markets? Think about retirement, even if you’re 18. It comes quicker than you may think. Then there’s taxes, shop overhead, and all the expenses. Don’t be over optimistic, be real.
Francis always said, “There’s room at the top,” implying those doing the highest quality work usually have work to do. And I imagine Francis was pretty good when WWII broke out, and he spent the War teaching welding 3000 miles from his Carmel shop. So, a person has to anticipate the unexpected life changing events. It all comes down to decisions. How much risk am I willing to take? And if the decision is made, give it all you got and then some!
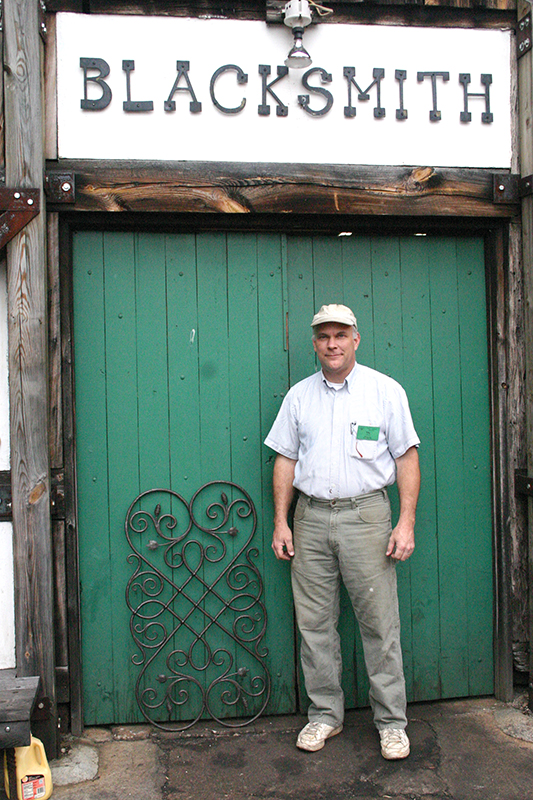
Tal Harris and Finished Project in Front of the Francis Whitaker Shop
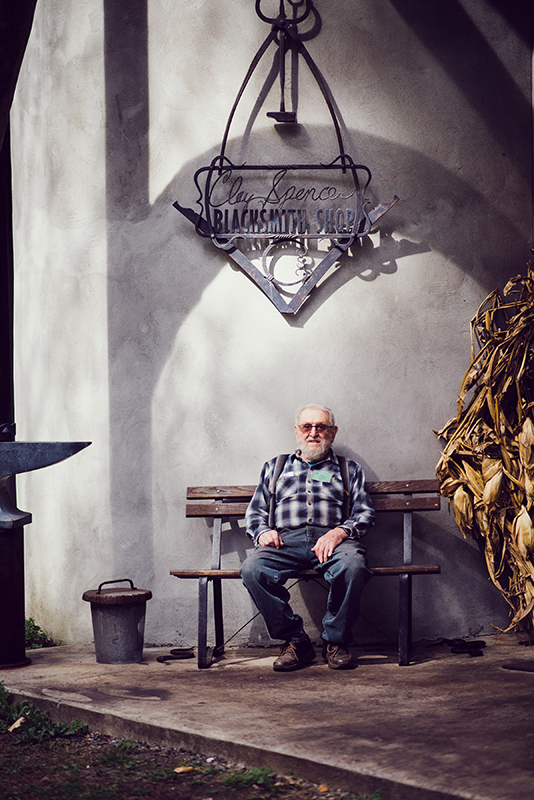
Clay Spencer in Front of the Clay Spencer Blacksmith Shop
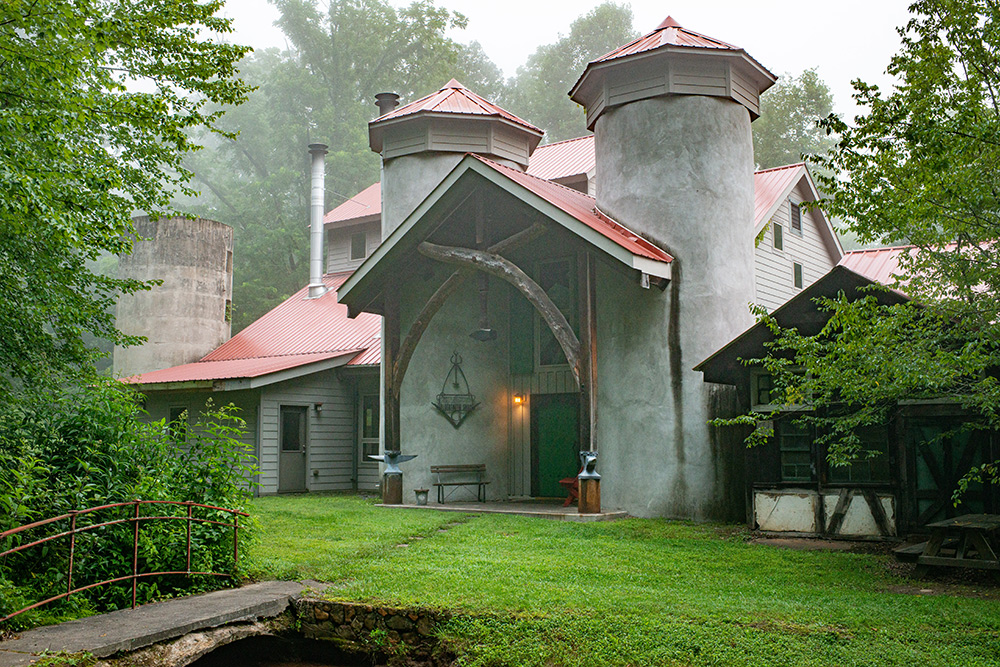
Our Clay Spencer Blacksmith Shop opened in 2009
Don’t Miss This Incredible Opportunity! View Upcoming Class Details
Advanced Blacksmithing
Following the tradition of Francis Whitaker, students will have the opportunity to focus on fine ornamental iron work for a personal, predesigned project. In addition to working on individual projects, students will share and learn from the techniques used in their fellow classmate’s work. Students must be able to perform a dropped-tongs forge weld, make upset square corners, and freehand scrolls. Predesigned projects must be submitted to instructors before class begins.
Notice: This Class Has Passed. Please check out our other Blacksmithing classes.
About Tal Harris
Tal Harris currently operates W. T. Harris Metalsmiths at his home in Clayton, NC. In addition to blacksmithing, he also has 42 years experience working with a company that makes high performance metals, primarily nickel and titanium alloys for the aerospace industry. Tal began blacksmithing in 1980 while attending Appalachian State University, and in 1982, he attended the Frank Turley School of Blacksmithing in Santa Fe for 6 weeks. Building on that foundation, classes were taken with Francis Whitaker, Clay Spencer, Peter Ross, George Dixon, and Tom Latane at the Folk School. Additionally, he has instructed at the John C. Campbell Folk School since the late 90s, and demonstrated at numerous Blacksmithing events, including the 1998 ABANA Conference in Asheville, NC. He also participated in special projects with Francis Whitaker at the 1994 and 1996 ABANA Conferences. In 2000 he led two one-week workshops in Queensland, Australia.

About Clay Spencer
Clay Spencer has been blacksmithing since 1987 and has demonstrated and led workshops for many blacksmithing groups and conferences. He served on the board of Artist-Blacksmith’s Association of North America (ABANA) and received their Alex Bealer Award and life membership. He is a lifetime member of the Alabama Forge Council and was editor of “Bituminous Bits” for ten years. Clay is also a lifetime member of the Blacksmiths Association of Missouri, the North Carolina Chapter of ABANA, and the Appalachian Area Chapter Blacksmiths. He previously served on the Folk School’s board of directors and has taught blacksmithing here since 1988. In 2010, the school’s new blacksmith shop was named in his honor. Having studied under Francis Whitaker, Clay is proud to carry on the teaching of traditional joinery techniques.
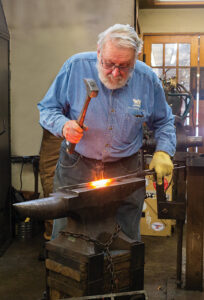
Francis Whitaker (1906–1999)
Francis Whitaker, known as the “Dean of American Blacksmiths,” devoted his life to keeping the art of blacksmithing alive in this country and the existing studio stands as his symbolic legacy.
Francis Whitaker was born November 29, 1906, in Woburn, Massachusetts. He left high school at the age of 16 to apprentice with the premier ornamental blacksmith of the day, Samuel Yellin, in Philadelphia. After a year with Yellin, Whitaker volunteered for a three-year apprenticeship in Berlin with the German master Julius Schramm. In 1927, he returned to the United States and settled in Carmel, California, where work was plentiful. In 1933, Whitaker opened his own forge, The Forge in the Forest, and despite the depths of the Great Depression he managed to build his own business. During World War II, he did production work and was the head instructor in welding at the Richmond Shipyards. As soon as war production work ended in 1945, he returned to his forge. In Carmel, Whitaker was active in local politics and was a pioneer conservationist. He was instrumental in ensuring that Point Lobos, a spectacularly scenic and biologically rich stretch of seacoast near Monterey, was designated a state reserve. In 1963, his efforts to protect Carmel’s sand dunes failed; disappointed, Whitaker closed his Forge in the Forest and moved his shop to Aspen, Colorado. There he received numerous private commissions, and in 1968 he began teaching at Colorado Rocky Mountain School, a private school in Carbondale, where he worked until his death on October 23, 1999.
Francis first came to the Folk School in the middle 1970s. He first taught at the small Oscar Cantrell shop where students had to bring their own forges. Starting in 1991, and finished in 1993, Francis led three workshops to build the chandeliers for the dining hall. The “Francis Whitaker Blacksmith Shop” was dedicated to him in 1993. The sign outside this shop was built the next year in 1994, which was built during a blacksmith work week.
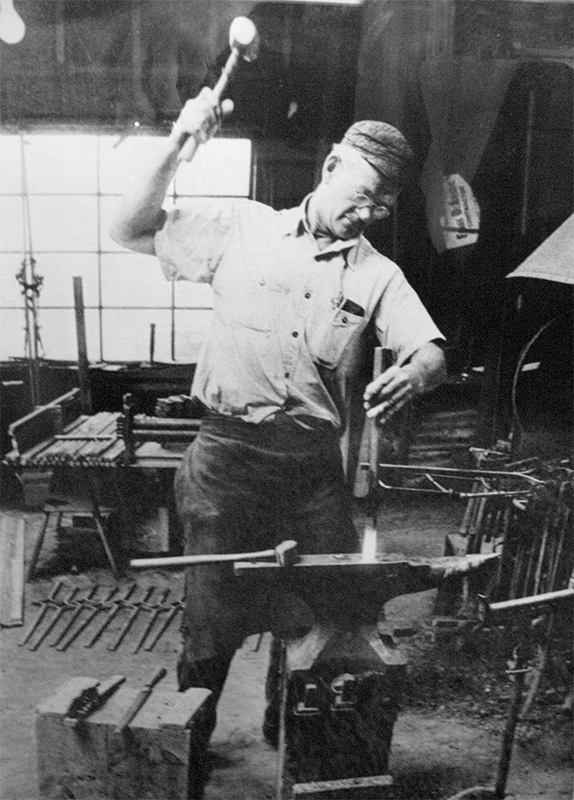
No Comments